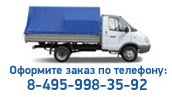
КАТАЛОГ
- Инструмент
- Сухие смеси
- Утеплители
- Гипсокартон
- Подвесы,крабы, профили, тяги, уголки, маячки
- Фанера
- Бетоноконтакт, грунтовки
- Цемент м-500, Смесь М-150, пескобетон м-300, связующие материалы
- Пиломатериалы
- Саморезы, дюбеля, гвозди
- Смеси для выравнивания полов
- Подоконники ПВХ
- Сетки малярные, стеклохост, серпянки
- Шпатлевки
- Теплый пол
- Металлы, Сетки металлические
- Штукатурки
- Электрика
- Гидроизоляционные материалы
- Затирочные смеси, добавки(затирочные)
- Монтажные пены, силиконы, жидкие гвозди
- Клея
- Алебастр
- Краски
- Кирпич, пеноблоки, газоселикатные блоки, ПГП
- Сыпучие материалы
- Цепи, Тросы
23 февраля 2019
Измерительный и разметочный инструмент
подробнее
21 января 2019
Монолитный бетон или кирпич
подробнее
19 января 2019
Какой дом выйдет дешевле и лучше
подробнее
12 января 2019
Ремонт квартиры для сдачи в аренду
подробнее
12 января 2019
Деревянные полы или деревянные панели?
подробнее
|
20 апреля 2011
Деревянные бревенчатые дома собирают на подготовленном и выверенном фундаменте. Перед монтажом на фундаменте устраивается горизонтальная гидроизоляция – наклеивается на мастике 2-3 слоя рубероида или другого рулонного гидроизоляционного материала.
На фундамент укладывается сухая доска толщиной 50 мм пропитанная антисептиком. Бревна для сруба необходимо подбирать по возможности с минимальной сбежистостью. Укладывают бревна в каждом следующем венце комлями в разные стороны. Бревна между собой по вертикали скрепляют нагелями.
При укладке каждого венца контролируют его горизонтальность и вертикальность стен и углов. Между венцами укладывают уплотнитель – мох, пакля или льноватин. Высоту сруба необходимо предусматривать из расчета его осадки на 3%. Устанавливать столярные изделия, монтировать балки пола и перекрытия желательно после осадки сруба. Высоту проемов для установки столярных изделий также надо предусмотреть с учетом осадки.
После полной осадки сруба необходимо провести конопатку уплотнителя, использую деревянную лопатку (конопатку) и киянку.
Монтаж стен деревянных брусчатых домов.
Брусья брусчатых стен кладут на фундамент по гидроизоляции из рубероида (2-3 слоя), уложенного на мастике. Нижние ряды брусьев должны быть проантисептированы.
Монтаж стен деревянных каркасных домов.
Стены каркасных домов состоят из рам, собираемых из брусков сечением 50х80 или 50х100 мм на гвоздях. На фундамент, выверенный по горизонтали, кладут гидроизоляцию.
Монтаж стен деревянных щитовых (панельных) домов.
Стены таких домов собирают из утепленных щитов. С наружной стороны щиты (панели) обшивают строганной обшивкой, с внутренней – твердой древесноволокнистой плитой или сухой гипсовой штукатуркой.
20 апреля 2011
Законченный архитектурный вид интерьеру помещения может придать устройство подвесных потолков из акустических и декоративных плит. Между подвесными потолками и перекрытием можно расположить электрическую и телефонную разводку, вентиляционные короба, различные трубопроводы.
Устройство таких потолков позволяет исключить «мокрые» процессы в отделочных работах, улучшить качество лицевой поверхности потолка, повысить производительность труда рабочих.
Основанием для подвесного потолка служит деревянный или металлический каркас, закрепляемый к перекрытию либо с помощью закладных деталей, устанавливаемых в швах между плитами перекрытия, либо дюбелями с помощью строительных пистолетов. Несущий каркас подвесного потолка с направляющими двутаврового профиля:
1 — направляющий элемент каркаса двутаврового алюминиевого профиля; 2 — плита «Акмигран»;
3 — фибровая шпонка;
4 – гребенка;
5 — нижняя часть подвески — скоба;
6 — верхняя часть разъемной подвески из стальной полосы; 7— закладной анкер;
8 — прогон из уголка; 9 — плита потолочного перекрыли;
10 — болт с гайкой для регулирования установки подвесного каркаса;
11—соединительная накладка;
12 — хомут
Облицовывая потолок плитами «Акмигран» по металлическому каркасу, их крепят с помощью алюминиевых направляющих в виде двутавра высотой 3 см с полкой шириной 2 см, которые монтируют к ранее установленным прогонам металлического каркаса.
Алюминиевые направляющие прикрепляют к прогонам металлического каркаса с помощью специальных подвесок, одновременно фиксируя гребенкой-шаблоном постоянное расстояние между направляющими, равное 600 мм. Затем устанавливают металлические погонажные детали или устраивают штрабы глубиной 20-30 мм для опирания фризовых панелей.
Плитки предварительно сортируют на столе-верстаке с помощью шаблона по размеру, тону и направлению волокон. Затем плиты заводят пазами на полки алюминиевых направляющих. Вставленные плитки поочередно продвигают по направляющим, заполняя между ними пространство.
Плитки соединяют пластмассовыми шпонками, устанавливаемыми в специальные пазы по две шпонки на каждую плитку. При этом смежные плитки должны плотно прилегать друг к другу без щелей и просветов. Потолок заполняют плитками рядами, начиная от одной из стен по направлению к противоположной.
Окончательная отделка подвесного потолка из акустических плиток заключается в окрашивании водоэмульсионными синтетическими красками.
Потолки из гипсовых акустических перфорированных плит устраивают в помещениях, где относительная влажность воздуха не превышает 70%.
20 апреля 2011
Основаниями под дощатые полы служат: бетонная подготовка, кирпичные столбики или цементная стяжка. Дощатые полы настилают из полового бруса, который изготовляют из досок толщиной 30-40 мм.
В одной кромке доски выбирают паз, в другой устраивают гребень. Одну из поверхностей доски прострагивают, другую – антисептируют. Влажность досок при их укладке должна быть не более 12%.
Половой брус настилают по лагам, представляющим собой брус или пластину. Лаги укладывают с шагом 0,6-0,8 м в зависимости от толщины полового бруса на подкладки из древесно-волокнистых плит. Между подкладками и основанием укладывают насухо один слой рубероида или пергамина.
Поверхность уложенных лаг выверяют по уровню. При настилке полов в комнатах лаги располагают перпендикулярно падающему из окон свету, при настилке полов в коридорах – перпендикулярно движению.
Половой брус устанавливают перпендикулярно лагам и соединяют между собой в шпунт. Гвозди забивают наклонно, с втапливанием шляпок в древесину. Для сплачивания досок при пакетном способе настилки применяют сжимы различных конструкций (ваймы, строительная скоба, сжим-скоба Смолякова и другие).
В плинтусах оставляют отверстия для вентиляции подпольного пространства. Дощатые полы красят за два раза после выполнения всех работ в помещении.
В набор ручного инструмента для настилки полов входят: ножовка, топор, молоток, гвоздодер, рубанок, уровень, складной метр,.
Производство работ при устройстве паркетных полов. Основанием под паркетный пол служит сплошной дощатый настил по лагам (черный пол) или стяжка (цементная или асфальтовая).
Паркетное покрытие пола может быть выполнено штучным паркетом, паркетными досками и паркетными щитами. Паркетные щиты и доски состоят из основания и паркетного покрытия. Основание выполняется из низкосортной здоровой древесины, покрытие – из ценных сортов лесоматериалов.
Все элементы щитов склеивают водостойкими клеями в заводских условиях. Паркетные доски или щиты укладывают непосредственно по лагам.
Горячие мастики подают на рабочее место в электротермосах и разливают ковшами сразу под две-три клепки. Холодные мастики разливают полосой по ширине клепки. Их укладывают по шнуру, поверхность проверяют рейкой.
К дощатому основанию паркетные клепки крепят гвоздями. Настилку начинают с маячного ряда так же, как и в предыдущем случае. Каждую клепку прибивают тремя гвоздями, забивая их в пазы клепок по одному с торца и по два – с длинной стороны, утапливая шляпки в древесину добойщиком.
Щитовой паркет и паркетные доски при укладке на стяжки или черный пол крепят аналогично отдельным клепкам, при укладке по лагам – аналогично дощатому полу. После настилки паркета его поверхность строгают паркетно-строгальной машиной, шлифуют паркетно-шлифовальной машиной и натирают воском или покрывают лаком.
Производство работ при устройстве полов из линолеума. Основаниями под полы из линолеума могут служить различные стяжки, черный или чистый дощатый пол. Линолеум на войлочной или губчатой основе укладывают непосредственно по плитам перекрытий. Под безосновный линолеум или под линолеум на тканевой основе по стяжкам укладывают два слоя древесноволокнистых плит.
Линолеум наклеивают на битумных, резино-битумных и масляно-меловых мастиках. До укладки линолеум распаковывают и выдерживают в вертикальном положении в сухом помещении при температуре не ниже +10 0С. Раскрой и раскладку линолеума насухо производят за сутки до его приклейки. Раскраивать следует так, чтобы в местах стыков листы линолеума перекрывались на 10 мм. За 30-40 минут до наклейки линолеума поверхность основания должна быть прогрунтована.
Клей или мастику наносят слоем не более 1,5 мм. Одновременно с наклейкой линолеум разравнивают и прижимают к основанию движением резинового валика от середины полотнища к краям для ликвидации воздушных пузырьков между основанием и линолеумом.
При применении “чехословацкого метода” наклейки линолеума стяжку шпаклюют казеино-цементной мастикой, а также наносят мастику на тыльную сторону линолеума. Через сутки поверхность прошпаклеванного основания шлифуют и вторично покрывают мастикой. Линолеум укладывают сразу после промазки основания.
Производство работ при устройстве полов из керамических плиток. До начала работ по укладке плиточного покрытия проверяют качество выполненного основания. Подготовка основания к облицовке заключается в очистке поверхности от пыли, грязи, остатков раствора, проверке уклонов и выверке углов помещения, что выполняют путем замера длины диагоналей.
Затем укладывают маяки и разбивают фризы. Фризы выкладывают из одного или нескольких рядов плиток, цвет которых отличен от цвета основного покрытия. Для обеспечения горизонтальности плиточного пола и устройства его на уровне, предусмотренном проектом, используют реперы, от отметки которых выставляют маяки и марки. Приступая к работе, закрепляют первую марку, устанавливаемую у стены, затем с помощью рейки и уровня остальные.
При выполнении плиточных покрытий иногда с помощью нивелира наносят отметки на всех стенах и по рейке соединяют их горизонтальной четной, тем самым создавая ориентир не только для плиточников, но и бетонщиков, которые делают подстилающий слой.
Маяки выполняют из плиток, укладываемых на жестком цементном растворе. Плитки вначале устанавливают несколько выше, а при выверке по уровню осаживают до нужной отметки легкими ударами молотка. Маяки подразделяют на маяки реперные (устанавливаются непосредственно у стены по вынесенной отметке чистого пола), фризовые (размещаются в углах и на линии фризов) и промежуточные (в больших помещениях). Для повышения производительности труда при устройстве плиточных полов используют рейки – шаблоны длиной 2-2,5 м с разметкой положения 20-25 плиток и швов между ними (рейки Болотина и др.).
После установки маяков настилают плиточные фризовые ряды, затем поперек помещения через каждые 20-30 плиток укладывают так называемые провески – ряды плиток, идущие параллельно одному из фризов.
Плитки укладывают вдоль длинной стороны помещения отдельными полосами – захватками. На первой захватке уширяют фриз и ведут заделку в направлении одной из продольных стен; вторая захватка следует за захваткой первой по направлению к дверному проему; третья и четвертая захватки – зеркальны по отношению к первой и второй. В последнюю очередь укладывают плитки на пятой захватке. Как правило, ширина захватки от 20 до 60 см.
Швы между плитками можно выправлять до начала схватывания раствора. После укладки 20-30 плиток их выравнивают с помощью ударов молотка по поверхности деревянного бруска, укладываемого по плиткам. Захватки, как правило, разделяют шнуром-причалкой, который крепят с помощью штырей, а в промежутках между штырями – стопками плиток, подкладываемых через каждые 25 плиток.
Звено плиточников, как правило, состоит из трех человек: плиточник 4-го разряда, который проверяет правильность формы пола и уклоны, определяет ширину фриза, устанавливает маяки и границы захваток, укладывает фризовые ряды; плиточник 3-го разряда, который разравнивает раствор, укладывает плитки между фризами и стеной, и плиточник 2-го разряда, который выполняет вспомогательные операции, разбирает плитки, заполняет швы между плитками и др.
На рабочем месте плиточника при настилке пола должны иметься низкая скамеечка, ручной инструмент, располагаемый на полу рядом с плиточником, запас раствора в ящике, располагаемом сзади рабочей зоны, плитки, подготовленные для укладки, разложенные стопками на свежеуложенных плитках последнего ряда.
Широко применяют метод настилки полов из керамических плиток пакетным способом с помощью шаблона. Применение этого метода позволяет повысить качество работ, увеличить производительность труда и снизить трудоемкость работ.
Плитки укладывают в шаблон лицевой стороной по 50 штук. Шаблон имеет ограничители ширины шва между плитками. После укладки плиток в шаблон пропускают запорные стержни через скобки. Этим заканчивается подготовка шаблона с плитками к укладке.
Шаблон подносят к месту укладки, поворачивают его на 180 град и затем осторожно опускают на раствор, вплотную к ранее уложенным плиткам. После правильной подгонки шаблона к ранее уложенным плиткам снимают все запорные стержни, слегка постукивают по шаблону и затем его снимают. После снятия шаблона производят отделку пола путем заполнения швов между плиткам жидким цементным раствором. На следующий деть пол поливают горячей водой и очищают от остатков раствора.
При большом объеме работ необходимо иметь два шаблона – один находится в работе, а другой в это время заполняется плиткой.
Ламинированные покрытия устраивают из плит размером 1200х400 мм, представляющих собой прессованную ДСП толщиной 7 м, облицованную синтетической пленкой с рисунком. Оно имеет вид полированного дерева. Соединение шпунтовое. С двух сторон – гребень, в остальных – паз. Материал экологически чистый и износоустойчивый. Может применяться во всех помещениях, где температура воздуха не ниже +18 град., за исключением помещений с повышенной влажностью (ванные комнаты, кухни, сауны и т. д.).
Ламинированные полы очень удобны в обслуживании, их можно мыть. Наилучшие условия эксплуатации полов при температуре +20 град. и влажности 50-60%. В отопительный период влажность в помещении существенно понижается, поэтому рекомендуется применять увлажнители воздуха, чтобы избежать экстремального высыхания пола.
Ламинированные полы следует укладывать на ровную поверхность. Это может быть линолеум, паркет, наклеенный войлок и т. д., кроме ковролина. Ковролин необходимо удалить. Если полы бетонные, надо застелить их полимерной пленкой толщиной 0,2 мм. Края пленки должны быть приподняты на 2 см (эффект ванны) и склеены. Большие неровности на основаниях под покрытие надо зашпатлевать или сошлифовать. Небольшие неровности выравнивают оргалитом, картоном для пола, пленкой из искусственного материала.
Ламинированные полы укладываются «плавающим» образом (не закрепляя к основанию), при изменении влажности они могут расширяться и сжиматься. Помещения площадью более 100 кв. м или помещения, в которых длина одной стороны составляет более 10 м должны быть разделены швами. В этом случае рекомендуется площадь пола разделить на секции размером 10х10 м, а швы после укладки плит закрыть изоляционной пленкой и планками.
Перед началом работ материал нужно выдержать при комнатной температуре в течение 48 часов. Затем все панели проверить на отклонение от горизонтальной плоскости, отклонение не должно составлять более 1 мм. Основание должно быть гладким, сухим, чистым, жестким. Первая панель укладывается в углу абсолютно ровно с зазором от стены 10-15 мм. Для этого используют деревянные клинья. Затем натягивают в двух направлениях шнур-причалку. Помимо шпунтового соединения панели склеивают между собой клеем ВЗ-«ANALITAT».
Клей наносят тонким слоем по долевой и поперечной сторонам панелей и их быстро соединяют друг с другом. Между ними не должно быть никаких, даже тонких щелей. Для подстукивания панелей при их соединении лучше использовать кусочек дерева из остатков от панелей. Нельзя стучать молотком по ребрам щели. Излишки клея, которые выступают из щелей, удаляют шпателем через 15 минут. Клей между панелями плотно загустевает и предохраняет швы от влаги.
15 апреля 2011
Известно, что бетон, как материал конструкции плохо сопротивляется растягивающим напряжениям, которые возникают в конструкциях неизбежно. Для восприятия растягивающих напряжений используют арматуру из материалов, хорошо сопротивляющихся растяжению.
В качестве таких материалов используют в первую очередь сталь и в ограниченных размерах – неметаллическую арматуру. Надо кстати заметить, что иногда в тяжелонагруженных конструкциях, особенно при невозможности увеличивать размер их сечений, арматура воспринимает также и сжимающие усилия.
В качестве материала неметаллической арматуры используются стеклопластиковые прутья для стержневого армирования и рубленое синтетическое или асбестовое волокна при дисперсном армировании. Эти стройматериалы прочны, не подвержены коррозии, но некоторые их свойства делают проблематичным их массовое использование для армирования бетона.
Исключение – асбестоцементные конструкции. Особенно незначителен опыт использования неметаллической арматуры в построечных условиях, которые рассматриваются в настоящем разделе курса. Поэтому пока исключим неметаллическую арматуру из нашего рассмотрения.
Стальная арматура может быть использована для:
линейного армирования – отдельными прутьями, арматурными прядями, канатами, отдельными проволоками и проволочными пучками;
плоского армирования – плоскими арматурными каркасами или сетками;
объемного армирования – объемными арматурными каркасами;
дисперсного армирования – рубленой проволокой диаметром до 2,5 мм.
При изготовлении железобетонных конструкций применяют отдельные арматурные изделия – закладные детали и монтажные элементы.
Для армирования железобетонных конструкций применяется арматура, отвечающая требованиям одного из следующих нормативов: СНиП 2.03.01-84*.
Бетонные и железобетонные конструкции (старая НТД) или ГОСТ 10884-94 (новая НТД).
Согласно СНиП используется:
- стержневая арматурная сталь горячекатаная гладкая класса A-I; - стержневая арматурная сталь горячекатаная периодического профиля классов A-I, A-II, A-III, A-IV, A-V и А-VI; - стержневая арматурная сталь термически и термомеханически упрочненная периодического профиля классов Aт-IIIС, Aт-IV, Aт-IVС, Aт-IVК, Aт-V Aт-V Aт-VК Aт-VСК Aт-VС, Ат-VIК, Aт-VII; - арматурная холоднотянутая проволока обыкновенная периодического профиля класса Вр-I; - арматурная холоднотянутая проволока высокопрочная гладкая класса В-II; - арматурная холоднотянутая проволока высокопрочная периодического профиля класса Вр-II; - арматурные канаты спиральные семипроволочные класса К-7; - арматурные канаты спиральные девятнадцатипроволочные класса К-19.
Допускается применять также арматуру других видов, в том числе после упрочнения вытяжкой на предприятиях стройиндустрии, класса А-IIIв. В обозначении классов термически и термохимически упрочненной стержневой арматуры с повышенной стойкостью к коррозионному растрескиванию под напряжением добавляется буква «К», к свариваемой – буква «С».
В обозначении горячекатаной стержневой арматуры буква «в» употребляется для арматуры, упрочненной вытяжкой, а буква «с» – для арматуры специального назначения.
Сталь арматурную термохимически упрочненную, изготавливаемую по межгосударственному стандарту, также подразделяют на классы в зависимости от механических свойств и эксплуатационных характеристик. Арматурную сталь изготавливают классов Ат400С, Ат500С, Ат600, Ат600С, Ат600К, Ат800, Ат800К, Ат1000, Ат100К, и Ат1200.
Классам арматурной стали по ГОСТ 10884-94 соответствуют следующие обозначении по СНиП 2.03.01-84: Ат400С – А-I, Ат500С – А-II, Ат600 – Ат-IV, Ат600С – Ат-IVС, Ат600К – Ат-IVК, Ат800 – Ат-V, Ат800К – Ат-VК, Ат1000 – Ат-VI , Ат1000К – Ат-VIК, Ат1200 – Ат-VI .
Арматурную сталь изготавливают с периодическим профилем согласно ГОСТ. Она представляет собой круглые стержни с двумя продольными ребрами или без них и с расположенными под углом к продольной оси стержня поперечными серповидными ребрами, идущими по многозаходной винтовой линии, имеющей на сторонах профиля разное направление. Профилирование арматуры осуществляется с целью увеличения сцепления ее с бетоном в конструкции.
Холоднотянутая арматура – проволока, упрочняемая в процессе протяжки через фильеры за счет получения наклепа, предел прочности такой арматуры зависит от ее диаметра – чем он меньше, тем выше предел прочности.
Для закладных деталей используется лист, прокатный профиль. Заводами изготавливаются рулонные и тканые сетки.
Арматурная сталь диаметром 6 и 8 мм поставляют в бухтах, что также допускается для стали классов Ат400С, Ат500С и Ат600С диаметром 10 мм.
Стержни изготавливают мерной длины от 5,3 до 13,5 м. Допускается изготовление стержней мерной длины до 26 м по требованию потребителя. Стержни упаковывают в связки массой до 10 т, перевязанные проволокой, по требованию потребителя – до 3 т. При поставке стали диаметром 5-8 мм в бухтах, каждая бухта должна состоять из одного отрезка арматурной стали, масса бухты – до 3 т.
Все арматурные работы можно объединить в две группы: предварительное изготовление арматурных элементов и установка их в проектное положение. Изготовление арматурных элементов производится, как правило, в заводских условиях централизованно и включает работы подготовительные и сборочные.
В состав подготовительных работ входят очистка, правка, резка, гнутье. Очистка, правка и резка на нужные размеры арматуры, поставляемой в бухтах, осуществляется на правильно-отрезных станках. Арматура из пачек режется арматурными ножницами различных конструкций. Гнутье арматурных заготовок осуществляется гибочными станками различных конструкций, начиная от ручных и заканчивая станками с компьютерным управлением.
При подготовке арматуры к сборке желательно пользоваться безотходными технологиями – из отдельных прутьев сваривается бесконечная плеть на стыкосварочной машине, а затем от нее отрезаются заготовки необходимых размеров.
Сборочные работы – это сборка плоских сеток и каркасов и сварка закладных деталей. Сетки и каркасы варятся контактной сваркой на одноточечных и многоточечных сварочных станках. Закладные детали – дуговой сваркой или контактной под слоем флюса.
На строительной площадке производится укрупнительная сборка арматурных элементов и подготовка арматуры, монтируемой отдельными стержнями, устанавливают (монтируют) арматурные блоки, пространственные каркасы, сетки, стержни, соединяют монтажные единицы в проектное положение в единую армоконструкцию.
При установке арматуры в опалубку особое внимание необходимо уделять обеспечению проектной толщины защитного слоя арматуры, для чего используются подкладки бетонные или проволочные (лягушки), металлические или пластмассовые фиксаторы. Стальные фиксаторы в виде удлиненных стержней и скобок выходя на поверхность бетона и поэтому коррозируют. Пластмассовые подвержены старению, деформируются под нагрузкой, что приводит к образованию трещин.
Этих недостатков лишены растворные фиксаторы, но они при вибрации могут менять положение, вызывая нарушение толщины защитного слоя.
Армирование предварительно напряженных конструкций производится либо с натяжением арматуры на бетон, либо на форму (электротермическое или механическое с использованием домкратов, гаек, зажимов различных конструкций).
Одним из видов предварительного напряжения арматуры является непрерывное армирование арматурной проволокой или проволочными прядями с помощью навивочных машин.
15 апреля 2011
Приготовление бетона осуществляется, как правило, на бетонных заводах, оборудованных механизированными и автоматизированными установками. Эти заводы могут быть в составе малых, средних и больших заводов ЖБИ, а также самостоятельными или выполненными в сборно-разборном варианте и эксплуатироваться непосредственно на строительной площадке.
Такие заводы, цеха, узлы выдают в зависимости от потребности либо бетонные, либо растворные смеси. Технологические схемы производства товарного бетона и раствора бывают одноступенчатыми (высотными) или двухступенчатыми
Кроме таких стационарных или сборно-разборных бетонорастворных узлов могут использоваться передвижные (мобильные) бетонорастворные установки, смонтированные на тяжелых автомобильных прицепах. Они обычно скомпонованы по двухступенчатой схеме.
Механизмом, определяющим качество бетонной смеси, производительность бетонного узла, периодичность работы, является бетономешалка.
Бетономешалки бывают гравитационного перемешивания (свободного падения составляющих) и принудительного. Гравитационные – с опрокидывающимся барабаном и с разгрузочным лотком. Бетономешалка принудительного перемешивания делятся на циклического действия и непрерывного. Наиболее распространенная бетономешалка принудительного действия – с вращающейся чашей, используется для приготовления жестких бетонных смесей.
15 апреля 2011
В настоящее время бетонную смесь доставляют от места приготовления до места ее укладки в конструкции автомобилями-самосвалами, специальными автомобилями-бетоновозами, в бадьях (бункерах), автобетоносмесителями (миксерами). Для транспортирования бетонной смеси используют также ленточные транспортеры и трубопроводный транспорт в сочетании с бетононасосами.
Во время транспортирования в целях сохранения однородности (исключения расслоения) и подвижности бетонная смесь должна быть защищена от попадания атмосферных осадков, вредного воздействия ветра и солнечных лучей, а также от утечки цементного молока. В зимнее время бетонную смесь при транспортировании необходимо защищать от замораживания. Для этой цели применяют специально утепленные виды транспорта. Кроме того, бетонная смесь должна доставляться к месту укладки без промежуточных перегрузок.
Исходя из этих условий, и принимаются разные виды транспорта.
Автомобили-самосвалы, а также бадьи и контейнеры могут использоваться при перевозке бетонных смесей на расстояние до 10-30 км. При этом самосвалы целесообразнее использовать при больших объемах бетонных работ и разгрузке смеси непосредственно в опалубку, т. е. при бетонировании конструкций, примерно на уровне земли, а бадьи – при бетонировании конструкций, расположенных выше уровня земли.
Автобетоновозы – это те же самые самосвалы и рациональная область его применения такая же. Отличается он от универсального автосамосвала конструкцией кузова: во-первых, от закрыт, во-вторых, форма кузова облегчает выгрузку и практически исключает прилипание бетонной смеси в углах ввиду отсутствия последних.
Автобетоносмесители – это специальный, качественно отличающийся вид транспорта, а значит и более дорогой. Это по существу бетоносмеситель на колесах, способный перемешивать смесь в процессе транспортирования, а значит исключить опасность расслоения. Он может перевозить не только готовые бетонные смеси, но и сухие смеси, добавляя них воду непосредственно при подъезде к строительной площадке, что практически неограниченно увеличивает возможные с технической точки зрения расстояния перевозки.
Способ транспортирования по трубам особенно эффективен для перемещения бетонной смеси в пределах строительной площадки. Он особенно широко стал применяться в комплексе с автобетоновозами и бетононасосами или автобетоносмесителями.
Бетоноукладчики, имеющие вылет стрелы до 60 м, устанавливают на смонтированные конструкции здания или вспомогательные опоры. На следующую стоянку бетоноукладчик, масса которого 1-6 т, переставляется установленным на объекте монтажным краном, бетоновод удлиняется и бетонная смесь подается на вновь возводимые ярусы здания.
При использовании трубопроводного транспорта актуальным становится применение литых бетонных смесей, перерасход цемента в которых исключается использование суперпластификаторов.
Все трубопроводы, насосы, бункера, укладчики после прокачки бетонной смеси промываются водой. Утилизация промывочных вод зачастую становится трудно решаемой проблемой на строительной площадке.
Для перекачки по трубам используют бетононасосы с механическим приводом, гидравлическим (поршневые) и пневмонасосы.
15 апреля 2011
Укладка бетонной смеси осуществляется различными способами, в зависимости от вида бетонируемой конструкции. Укладке бетонной смеси в опалубку должны предшествовать проверочные и подготовительные работы. Проверяют все основные отметки опалубки, правильность ее геометрических размеров.
Опалубку очищают от мусора, деревянную опалубку примерно за 1 час до бетонирования поливают водой, наносят антиадгезионную смазку. Проверяют и очищают арматуру, при соответствии ее требованиям проекта и технических условий составляют акт освидетельствования скрытых работ. Резьбовые части закладных и анкерных деталей смазывают солидолом. И только после этого можно приступать к бетонированию.
Основными технологическими требованиями к укладке бетонной смеси являются: обеспечение монолитности бетонируемой конструкции и необходимого уплотнения бетонной смеси.
Для обеспечения монолитности железобетонных конструкций бетонирование необходимо вести непрерывно. Однако это реально возможно только при небольших объемах работ. Во всех остальных случаях перерывы в бетонировании неизбежны.
Для того чтобы швы (стыки затвердевшего и вновь укладываемого бетона) не оказались в тех местах конструкции, где они угрожают ее несущей способности, необходимо заранее предусмотреть такие швы, чтобы обеспечить непрерывность бетонирования в пределах между ними. Такие заранее предусмотренные в безопасных местах швы называются рабочими швами.
Рабочие швы в вертикальных элементах должны быть горизонтальными, в горизонтальных – вертикальными. При наличии в конструкциях температурных и осадочных швов рабочие швы по возможности надо с ними совмещать.
Поверхности затвердевших рабочих швов подготавливают к укладке бетонной смеси следующим образом: очищают, продувают, делают насечку, непосредственно перед бетонированием покрывают цементным раствором толщиной 20-50 мм.
Уплотнение бетонной смеси в монолитных конструкциях осуществляют механически путем (трамбование, вибрирование, вакуумирование). При небольших объемах возможно ручное уплотнение трамбовками, шумовками, подбойками.
Наиболее широкое распространение получило виброуплотнение в силу его универсальности, простоты аппаратурного оформления способа. Способ основан на способности бетонной смеси к тиксотропному разжижению под воздействием вибрации.
Вибраторы бывают погружные (глубинные), наружные (навесные), поверхностные
15 апреля 2011
Технология бетонирования конструкций выбирается с учетом типа конструкции, ее расположения на здании или сооружении, климатических условий, наличия энергетических ресурсов и т. д.
Бетонирование ступенчатых фундаментов осуществляют в три приема. Вначале бетонируют нижние ступени, затем подколонник до гнездообразователя и далее – верх подколонника. Фундаменты, воспринимающие динамически нагрузки, бетонируются в непрерывном режиме. Бетонные полы, основания под полы, дороги бетонируют полосами шириной 3-4 м с установкой маячных досок.
Колонны бетонируют ярусами высотой до 5 м, а при сечении менее 40х40 см и с перекрывающимися хомутами – высотой до 2 м.
При высоте колонн свыше 5 м смесь подают через воронки по хоботам. Вначале бетонирования колонн (так же как и стен) нижнюю их часть заполняют на высоту 100-200 мм цементным раствором состава 1:2-1:3 (во избежание образования в этой части конструкций раковин бетона и скоплений крупного заполнителя).
Балки и прогоны бетонируют, как правило, одновременно с плитами перекрытия. Только при очень массивных балках (высота более 0,8 м) может быть допущено в виде исключения раздельное бетонирование. В таких случаях рабочие швы располагают несколько ниже плиты.
Бетонирование прогонов, балок и плит следует начинать через 1-2 часа после бетонирования колонн и первоначальной осадки в них бетона. Уплотнение бетона в балках и прогонах производится глубинными вибраторами. Если балки густо армированы, вибраторы оснащают наконечниками (виброштыки) или используют виброгребенки.
Плиты перекрытия бетонируют на полную высоту (толщину) и уплотняют поверхностными вибраторами. В балки (прогоны) и плиты ребристых перекрытий смесь укладывают, как правило, одновременно.
Своды небольших пролетов (до 15 м) бетонируют одновременно с двух сторон от пят к замку. Бетонирование всего свода на каждой секции должно быть выполнено без перерывов. При бетонировании сводов и арочных строений мостов пролетом более 15 м принимают меры против появления трещин из-за неравномерной осадки кружал и бетона. С этой целью своды и арки разбивают на отдельные участки (секции), между которыми оставляют небольшие разрывы шириной 30-50 см. На каждом участке смесь подают непрерывно.
Спустя 7-14 дней после затвердевания основных клиньев места разрывов бетонируют жесткой бетонной смесью, создавая как бы малые клинья. Разрывы желательно оставлять против стоек лесов или в узлах кружальных ферм. Клинья бетонируют с двух сторон от пят к замку, чтобы устранить вредные деформации кружал.
15 апреля 2011
Значительную долю жилищного строительства составляет строительство домов из сборных железобетонных и легкобетонных конструкций. В жилых зданиях преимущественно используют две конструктивные схемы: каркасно-панельную и панельную. Каркасно-панельная предусматривает передачу действующих нагрузок на каркас, который обеспечивает прочность и устойчивость здания.
При бескаркасной панельной схеме нагрузка воспринимается системой панелей (как правило, панелями поперечных стен и перекрытий). Поперечный модуль до 6 м определяет пролет перекрытий, а продольные модули до 3,6 м – разбивку проемов в наружных стенах. Все основные элементы здания – сборные железобетонные. Крупноблочные здания строят с продольными несущими стенами из легкобетонных блоков двухрядной разрезки. Перекрытия – железобетонные многопустотные плиты. Высотные дома (дома повышенной этажности) – преимущественно каркасные.
Сборные жилые дома из железобетонных конструкций – это, конечно, не единственный тип жилища. Достаточно много строится кирпичного жилья, в котором однако также не обходится без монтажа сборных конструкций – перемычек, перекрытий, лестничных площадок и маршей (лестницы из отдельных ступеней, уложенных по металлическим или железобетонным косоурам применяются только в зданиях, строящихся по индивидуальным проектам), лифтовых шахт, объемных блоков санитарно-технических кабин, вентиляционных блоков и шахт, железобетонных карнизов и балконов, сборных перегородок, т.е. современный кирпичный дом называть кирпичным можно достаточно условно. Монтажных работ и сборных конструкций в нем хватает.
В некоторых территориальных зонах страны, особенно в лесных районах, главным строительным материалом продолжает оставаться пиломатериалы. Но и здесь наряду с традиционными конструкциями из дерева (стены – срубы из бревен или бруса, перекрытия – деревянные по деревянным балкам) широкое распространение получают индустриальные конструкции – каркасно-щитовые дома и соответствующие индустриальные способы их возведения – монтаж из готовых укрупненных элементов.
Аналогичные конструктивные схемы зданий и аналогичный набор строительных конструкций используются при строительстве зданий социально-бытового и культурного назначения. В производственном строительстве несколько иные соотношения материалов и конструкций. В современном производственном строительстве практически не используется в качестве несущих и ограждающих конструкций древесина (за исключением, пожалуй, сельскохозяйственного производственного строительства, да и то в незначительных объемах).
Значительно меньший объем применения кирпича, особенно в конструкциях основных производственных цехов. Зато, с другой стороны, велик объем используемых для строительства производственных зданий металлических конструкций, особенно в покрытиях или перекрытиях большепролетных зданий, а основной все-таки материал сейчас – сборный железобетон. Хотя, как утверждают многие экономисты, это не всегда экономически целесообразно.
Основной конструктивной схемой многоэтажных производственных зданий является каркасная, с набором конструкций, аналогичным каркасным зданиям гражданского назначения. Одноэтажные промышленные здания строятся в основном на основе так называемых унифицированных каркасов. Основные элементы таких каркасов – колонны, подкрановые балки (если цех оборудован мостовыми кранами), подстропильные и стропильные конструкции, плиты покрытия, навесные или самонесущие стеновые панели, горизонтальные и вертикальные связи.
Все сборные конструкции должны при монтаже подниматься, перемещаться, удерживаться. Для этого они, естественно, должны быть закреплены к перемещающему органу грузоподъемного механизма. Поэтому подавляющему большинству строительных конструкций присуще общее качество – наличие специального места для захвата детали при подъеме. В большинстве типов изделий в этих местах установлены монтажные петли. Но наличие петель не всегда удобно или допустимо. Например, колонны, перекрытия. Тогда их можно либо спрятать (разместить в специально устроенных выемках), либо заменить отверстиями, штырями, либо использовать фрикционные или вакуумные захваты.
Значительно проще решаются вопросы строповки деревянных панелей или конструкций из металла. И в тех и в других специальных монтажных петель обычно не делают. Эти конструкции попросту привязывают, используя, как правило, универсальные или облегченные стропы. Строповку осуществляют в узлах конструкций, чтобы не создавать в процессе монтажа таких напряжений в элементах конструкций, которые могли бы привести к их повреждению или разрушению.
15 апреля 2011
При сборке конструкций здания из отдельных элементов в месте их соединения образуется стык. Одни стыки обеспечивают прочность соединения деталей, другие – герметичность.
Конструкции стыков, обеспечивающих прочность, применяемых в унифицированных каркасных системах, отличаются большим разнообразием.
Условно можно выделить следующие основные типы стыков, выполняемых посредством:
* сварки стальных закладных деталей или арматурных выпусков соединяемых между собой элементов; * введения фиксирующих штырей (выпусков) одного элемента в соответствующие гнезда другого элемента; * установки стяжных болтов; * обжатия зоны стыка с помощью напрягаемой на бетон арматуры.
Жесткие стыки всех типов обычно выполняются с последующим замоноличиванием. В последнее время начинают применять клеевые стыки на эпоксидных составах.
Примеры стыков, обеспечивающих прочность: * колонна с фундаментом; * колонна с колонной (наращивание); * колонна с ригелем; * плиты перекрытия со стеновыми панелями и между собой.
Закладные детали после сварки защищают от коррозии путем обетонирования всего стыка (иногда монолитный стык выполняется без сварки в крупнопанельном домостроении), окрашиванием масляными красками (стык ригелей и колонн), обмазкой цементным молоком (соединение плит перекрытий и ригелей), покрытием специальными казеино-цементными составами (соединение перемычек блоков между собой) или металлизацией закладных деталей (стыки крупнопанельных зданий).
Стыки, обеспечивающие герметичность соединения деталей, устраивают при соединении между собой блоков и панелей наружных стен. При заделке стыков крупноблочных стен полость, образованную фигурными торцами смежных блоков, заливают легким бетоном. В крупнопанельных стенах закрытую фигурную полость, образованную торцами смежных панелей, заполняют несколькими материалами, каждый из которых выполняет определенную функцию.
|