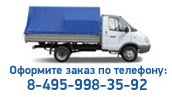
КАТАЛОГ
- Инструмент
- Сухие смеси
- Утеплители
- Гипсокартон
- Подвесы,крабы, профили, тяги, уголки, маячки
- Фанера
- Бетоноконтакт, грунтовки
- Цемент м-500, Смесь М-150, пескобетон м-300, связующие материалы
- Пиломатериалы
- Саморезы, дюбеля, гвозди
- Смеси для выравнивания полов
- Подоконники ПВХ
- Сетки малярные, стеклохост, серпянки
- Шпатлевки
- Теплый пол
- Металлы, Сетки металлические
- Штукатурки
- Электрика
- Гидроизоляционные материалы
- Затирочные смеси, добавки(затирочные)
- Монтажные пены, силиконы, жидкие гвозди
- Клея
- Алебастр
- Краски
- Кирпич, пеноблоки, газоселикатные блоки, ПГП
- Сыпучие материалы
- Цепи, Тросы
23 февраля 2019
Измерительный и разметочный инструмент
подробнее
21 января 2019
Монолитный бетон или кирпич
подробнее
19 января 2019
Какой дом выйдет дешевле и лучше
подробнее
12 января 2019
Ремонт квартиры для сдачи в аренду
подробнее
12 января 2019
Деревянные полы или деревянные панели?
подробнее
|
20 марта 2011
Процесс шпатлевания стен требует тщательной подготовки и правильного подбора стройматериалов.
В настоящий момент лидеры рынка предлагают большой ассортимент
разнообразных шпатлевок. Эти отделочные материалы могут быть произведены
как на основе олифы, так и на гипсовой, цементной или акриловой основе.
Масляно-клеевые шпатлевки не отличаются долговечностью и абсолютной
экологической безопасностью, поэтому при выполнении отделочных работ от
их использования стоит отказаться.
Сухие шпатлевочные смеси на основе цемента или гипса хорошо
подходят для выполнения отделочных работ, однако и у этих материалов
есть ряд недостатков, к которым можно отнести весьма ограниченный срок
годности, а также необходимость подбирать подходящую емкость для
разведения смеси.
Наиболее оптимальным вариантом для осуществления такой ремонтной
работы, как шпатлевка стен, является использование материалов на основе
акрила. Таким шпатлевкам свойственна долговечность и отличная
влагостойкость.
Определившись с выбором шпатлевочной смеси, необходимо тщательно
подготовить поверхность стен к проведению работ. Основа, на которую
планируется накладывать слой шпатлевки, должна быть очищена от пыли,
оставшейся краски, различных жировых или восковых пятен. Если штукатурка
не отличается прочностью и осыпается, то ее также следует удалить с
поверхности стены.
Стоит избегать нанесения шпатлевочной смеси на промерзшие стены.
Для лучшего результата шпатлевочных работ рекомендуется нанести на
основание грунтовку с помощью специального валика. При этом очень важно
обработать всю поверхность стены, нанося средство ровным слоем и не
допуская пропусков.
Шпатлевочную смесь подготавливают к работе в точном соответствии с
инструкцией на упаковке, после чего можно приступать к нанесению.
Обрабатывать следует увлажненную поверхность стены. Стоит также
отметить, что все шпатлевочные работы необходимо производить при
плюсовой температуре и уровне влажности, не превышающем 60 процентов.
При соблюдении этих условий материал удастся уложить ровным тонким
слоем, что обеспечит прекрасный результат на завершающем этапе.
Шпатлевку можно наносить как шпателем, так и с помощью специального распылителя.
При использовании пистолета-распылителя важно соблюдать технику
нанесения: после распыления состава на обрабатываемую поверхность
необходимо сразу разгладить наложенный слой с помощью резинового
шпателя.
Если шпатлевка стен изначально выполняется при помощи шпателя,
нужно соблюдать определенные правила работы. Сначала следует заполнить
составом все явные неровности и большие выемки и дать слою полностью
высохнуть. Только после этого можно приступать к наложению
выравнивающего слоя. При этом желательно использовать широкий шпатель,
изготовленный из нержавеющей стали, – это позволит достаточно быстро
обработать поверхность всей стены.
Кроме того, при выполнении шпатлевочных работ можно
воспользоваться и двумя шпателями, различными по размеру. Такая техника
нанесения состава позволяет равномерно распределить смесь без остатка и
сохранить инструменты относительно чистыми.
Для проверки правильности построения углов имеет смысл
воспользоваться строительным уровнем. Для оптимального выравнивания
углов лучше всего использовать угловой шпатель. Процесс шлифования
обработанной поверхности стены производится при помощи такого
инструмента, как шлифовальная терка. Стоит помнить о том, что шлифовать
необходимо каждый слой шпатлевки – это позволит добиться прекрасного
результата после завершения работ. Выполнять шлифовку можно только после
полного высыхания наложенного слоя.
Завершающие слои шпатлевки можно наносить при помощи резинового
шпателя, нанося перпендикулярные друг другу мазки. С помощью такой
техники достаточно легко удалить излишки материала и обеспечить
оптимальное выравнивание поверхности.
Особенно тонкого слоя наложения смеси можно добиться, расположив
шпатель под определенным углом. Особенно впечатляющие результаты дает
проведение работ под углом наклона шпателя в восемьдесят градусов.
После завершения ремонтных работ используемые инструменты нужно
тщательно промыть теплой водой. Избегайте попадания остатков
шпатлевочных смесей в канализацию – это может вызвать засорение труб.
Чтобы обеспечить наилучший результат работ, в течение нескольких
суток после их завершения необходимо поддерживать плюсовую температуру в
помещении и следить за тем, чтобы обработанная поверхность не
подвергалась переохлаждению. Излишне сухая среда также может оказать
негативное воздействие на обработанную поверхность, поэтому пересыхания
нанесенных слоев шпатлевки тоже следует избегать.
Через три-четыре дня можно приступать к завершающей обработке
поверхности стены – окрашиванию или оклейке выбранными обоями.
Шпатлевочные смеси и другие отделочные материалы дают возможность в
значительной степени выровнять стены, что позволит избежать проявления
дефектов при ведении работ по декоративной отделке.
Особенно важно
ответственно подойти к процессу шпатлевания стен в том случае, если вы
планируете установить в помещении нестандартную подсветку, поскольку
использование низкокачественных материалов и нарушение процесса укладки
слоев может дополнительно подчеркнуть существующие неровности и другие
недостатки. Не следует забывать и о том, что конструкции, изготовленные
из гипсокартона, также нуждаются в обработке шпатлевочными растворами.
Правильно выполненное шпатлевание стен с применением
высококачественных материалов создает прекрасные возможности для
разнообразной декоративной отделки помещения. Соблюдая технику нанесения
шпатлевочных составов, вы непременно добьетесь нужного вам результата,
который будет радовать вас долгие годы.
В нашем интернет магазине стройматериалов вы можете приобрести шпатлёвки: ветонит лр, ветонит кр, шитрок шпаклевка по самым выгодным ценам.
20 марта 2011
Строительная индустрия позволяет сегодня всем хозяевам квартир
чувствовать себя настоящими творцами своего интерьера, так как для них
созданы все условия для реализации даже самых причудливых фантазий.
К
примеру, многие отказываются от использования обоев в качестве
оформления стен в комнатах и по современному дизайну заменяют их на
покраску стен. Такой способ декорирования помещений представляет собой
гораздо большее разнообразие в плане выбора цветовой гаммы, текстуры и
характера оформления. Более того, он станет самым идеальным вариантом
для тех, кто любит часто делать перестановки квартиры и менять стиль
оформления помещения.
При помощи краски для стен можно создать любую цветовую палитру.
Если обои невозможно подобрать исходя из своих индивидуальных
предпочтений, и выбрать именно тот оттенок, который Вам нравится, то с
краской никаких проблем не возникнет. Строительная индустрия даже
предложит Вам услугу по колировки краски, во время такой процедуры Вы
сможете получить любой оттенок на Ваш вкус. Можно даже заранее прийти в
магазин с выбранным Вами оттенком и в колировочном каталоге выбрать тот,
который будет тон - в тон повторять цвет Вашего дивана.
Как сделать правильный выбор среди многообразия предложение?
Этим вопросом задаются все: и дизайнеры по украшению помещений и
сами хозяева квартир. Мода по покраску стен сделала отрасль производства
лакокрасочной продукции довольно – таки прибыльной и теперь уровень
конкурентных предложений в этом сегменте неуклонно растет, что позволяет
покупателям делать выбор в отличном соотношении цены и качества. Более
того, можно найти сезонные скидки на краски определенных марок, можно
воспользоваться скидками, которые предлагают покупателям магазины при
покупке нескольких продуктов.
Словом, Вам стоит определиться только с
цветовой гаммой и далее привлечь себе на помощь консультанта магазина с
красками, который расскажет в подробностях все об интересующей вас
продукции. Стоит обратить внимание, что очень популярные краски для стен
на сегодня имеют специфическую текстуру и могут даже создавать на
поверхности стен рисунок и рельеф. При покупке такой продукции стоит
обратить внимание на ее срок годности и также проконсультироваться у
продавца, по какой технологии и с использованием каких дополнительных
средств лучше всего делать работу по покраске помещения.
Не стоит стесняться и просить продавца показать сертификаты
соответствия на продукцию, ведь окраска стен в помещении не должна потом
стать причиной головной боли для домашних и гостей, которые будут к Вам
приходить. Если краска была изготовлена без соблюдения должной
технологии и не прошла необходимые проверки, это значит, она
потенциально опасна и от такой покупки лучше воздержаться. То же самое
относится и к средствам, которые Вы будет использовать непосредственно в
процессе покраски стен. Не стоит покупать с истекающим сроком годности
растворители, не стоит экономить на кисточках и валиках, ведь от их
работы и качества будет зависеть в целом восприятие и качество
отделочных работ в Вашей комнате.
Покраска стен своими руками
Как только Вы определитесь с цветом краски для стен, с ее
фактурой и дополнительными приспособлениями, которые помогут Вам
выполнить работы, наступит самое время приступить к процессу покраски
стен. Можно взять на вооружение советы тематических программ по ремонту,
можно посмотреть рекомендации на тематических форумах в интернете.
Особенно стоит обратить внимание на статьи, в которых есть рекомендации с
видео – сюжетами, в которых поэтапно и наглядно показаны все процессы
покраски стен. Здесь работает принцип наглядности, ведь если Вы увидите,
как правильно делает все действия по покраске мастер, Вам будет проще
повторить всю последовательность действий.
Начальный этап – это подготовка к покраске помещения, в котором
Вы собираетесь окрашивать стен. Выносим мебель или сдвигаем ее к центру
комнаты, накрываем вещи специальными чехлами для того, чтобы избежать
попадания на них капель краски. Проход к стене должен быть достаточным
для того, чтобы можно было при необходимости поставить стремянку и
прокрасить самые высокие уголки стен. Далее - снимаем со стены или
закрываем специальными ширмами ручки, розетки и переключатели. Предметы,
которые нет возможности передвигать, закрываем щитами. Для батарей есть
возможность купить специальные чехлы, которые после покраски можно
снять.
Теперь приступаем к основному кругу работ - очищаем поверхность
стены. Если до этого у Вас были обои, то стоит их тщательно смыть и
сделать поверхность совершенно ровной. Для этой процедуры стоит
применить мыльный раствор. Если до Вашей покраски на стене было
несколько слоев обоев, то для более тщательной очистки пригодится щетка с
жесткой щетиной. В любом случае стоит обработать стену дезинфицирующим
раствором, так как это позволит обеспечить стерильность и не позволит со
временем появиться на стенах грибку и плесени. Многие пренебрегают
такой простой и эффективной процедурой, но со временем жалеют об этом.
После очищения стены наступает ответственный момент –
выравнивание поверхности стены, при котором будут устранены все дефекты и
как результат – получена ровная поверхность стены. Идеальным помощником
в этой процедуре станет шпаклевка.
Затем наступит самый ответственный и требующий качественного
выполнения всех действий этап – покраска стен. Подготавливаем
инструменты для покраски. Вам понадобиться малярный лоток для краски,
валик для нанесения состава на стену, а также кисточка для прокрашивания
труднодоступных участков. В помещениях с высокими потолками также
пригодятся стремянка, специальный скотч защитный, который не позволит
запачкать краской потолок и малярный скребок, который поможет снять с
поверхности лишние капельки краски.
После того, как Вы равномерно окрасите стены, придирчиво
осмотрите сделанную Вами работу - если найдете какие-то недостатки и
недочеты, лучше всего устранить их, так как после высыхания краски их
будет уже устранить труднее. Секретным оружием станет использование
увлажненной тряпки.
В нашем интернет магазине стройматериалов вы можете подобрать себе любые краски по самым выгодным ценам!
19 марта 2011
Шумный город, плохая экология и бешенный ритм жизни утомляет
многих людей. Единственное спасение от всего этого можно найти на даче.
Начиная с весеннего периода и заканчивая поздней осенью, люди
стремятся проводить больше всего времени именно там. К сожалению, не на
всех дачных участках имеются дачные домики. А ведь это очень удобно и,
кстати, совсем недорого его построить. Благодаря разнообразным
магазинам, строматериалы есть на каждый вкус и кошелек.
Небольшой домик по силам построить любому хозяину. Конечно,
возвести особняк, одному не получится, но небольшой дом вполне
реально. Как говорится – главное начать.
До того, как завести стройматериалы на участок, следует построить
забор. В наше время он нужен, даже если дом и не планируется. Ведь мало
кто обрадуется, приехав на дачу за помидорами, обнаружить пустые
кустарники. А если начинается стройка, то соответственно и
стройматериалы будут находиться именно там. Забор, может быть каким
угодно: металлопрофильный, бетонный или кирпичный. Все зависит от
возможностей.
После того, как забор установлен, самое время подумать о
технологии, по которой будет возводиться дачный дом. Этому следует
уделить особое внимание и определиться с его назначением. Существуют
простые домики, исключительно для летнего отдыха, а есть и такие,
которые пригодны для постоянного проживания.
В основном дачные домики - это деревянные строения, которые
бывают: щитовые, каркасные и срубы. Самым недорогим и простым вариантом,
считается щитовой дом. Их монтаж очень прост, не требует особого
фундамента, да и в отделке он несложный. Но подходит такой дом для
проживания в теплое время года.
Каркасный дом это более сложная и практичная конструкция. Ведь в
нем можно проживать и зимой, и летом. И возвести такой дом дешевле, чем
из бруса. Поэтому такая технология сейчас пользуется популярностью.
Брусовые дома славятся своими удивительными свойствами и
долговечностью. Они поддерживают идеальный микроклимат внутри, в них
тепло зимой и прохладно летом. А смолы, которые содержатся в брусе, не
позволяют появляться болезнетворным бактериям.
Но прежде чем начать возводить дом, нужно помнить, что у любого
строительства должен быть план. Для того чтобы его сделать, нужно
ответить себе на несколько вопросов: что ожидается от новой дачи?
Сколько человек будет приезжать, и какого возраста? и будут ли еще на
участке другие постройки. На основе этих ответов, уже можно мысленно
прикинуть, какие удобства нужны в доме, сколько комнат потребуется и
какого должен быть размера дачный дом.
Далее свое внимание нужно уделить грунту. Такие технические
моменты очень важны, ведь именно от них будет зависеть долговечность
дачного дома. От грунта зависит, подойдут ли выбранные строительные
материалы или нет. Так же стоит уделить внимание канализации,
электроэнергии и к проводке телефона. А самое важное, определиться,
будет ли дом отапливаться, и каким методом. Все эти моменты очень важны
для будущего.
При строительстве дачного дома, нужно помнить о некоторых нюансах, которые возможно, повлияют на выбор стройматериалов.
1) Выбирая технологию строительства, нужно помнить о зимних
заморозках, так как в зимнее время года, не отапливаемый дом будет
проморожен. Поэтому здесь важно обратить внимание на силовую конструкцию
домика, которую от мороза может повести. В этом плане каркасно-щитовой
дом очень хорош, поскольку он может выдержать любые перепады температур.
2) Дачный дом должен создавать прохладу летом и тепло зимой. Для
этого можно выбрать конструкцию дачного домика с низкой
теплопроводностью. В этом случае снова каркасно-щитовой дом будет
оптимальным вариантом.
3) Так же нужно предусмотреть возможность разового отопления
дачного домика, в случае неожиданного похолодания в теплое время года.
Обычно это электрообогреватель.
Определившись с технологией, можно приступать к возведению. Как и
обычный дом, дачный домик нуждается в фундаменте. Самый популярный это
ленточный тип фундамента. Но, к сожалению, он подходит не для всех. У
обладателей участка, который расположен в низине и имеется постоянная
влажность, придется делать столбчатый фундамент. Он немного сложнее при
возведении, но намного надежнее.
После того как фундамент возведен и построен дом по выбранной
технологии, самое время заняться кровлей. Ежегодно появляются новые
материалы, которыми можно накрыть крышу. Среди них профнастил,
маталлочерепица, шифер и цементно-песчаная черепица. Это неполный список
всех видов кровли, поэтому не стоит останавливаться на первом же
понравившемся виде. Узнав подробнее недостатки и преимущества каждого
материала, можно делать вывод.
Дом построен, крыша есть и наступает самый приятный момент при
строительстве дома – его отделка. Вот тут точно есть, где разгуляться.
Ведь разнообразные строительные материалы позволяют включить свою
фантазию и выделить свой дачный дом. Для тех, кто не ищет сложных путей,
предлагается обшить свой дом сайдингом. Дом в такой «обертке» выглядит
очень красиво и аккуратно. Внутри, кроме простой покраски или
гипсокартона, можно воспользоваться и вагонкой. В любом случае, выбор
материалов зависит от личного вкуса и средств.
Существуют определенные требования и к инженерным сетям. Для того
чтобы проживание стало удобным и надежным, нужно обеспечить
электричеством весь дом. Особое внимание уделить мощности. Нужно
рассчитать, сколько будет требоваться электроэнергии на то или иное
оборудование.
Так же к инженерным сетям относится и водопровод. В этих
случаях частенько бурят скважину, вода из которой используется в
технических целях. Помимо воды, нужно позаботиться и об отводе всей
влаги от дома. Лучший вариант это канализационная система. Она позволяет
избавляться от двухсот литров воды на человека в день. Последним
штрихом будет обеспечение телевидением и Интернетом.
После того, как все готово, стоит позаботиться и о приусадебном
участке, который будет радовать глаз и создавать уют всей территории
дачи.
18 марта 2011
Евроремонт – это не только первый шаг к уюту в квартире, но и
возможность сделать жилье стильным и модным. В евроремонте используются
современные технологии и новейшие стройматериалы.
Чтобы ремонт не растянулся на неопределенный срок, нужно четко
заранее продумать все вопросы. Необходимо составить план, взвесить
возможные риски, сделать финансовые подсчеты, а затем приступать к
серьезным масштабным работам.
Выбор дизайнера.
Евроремонт в квартире необходимо начинать с выбора дизайнера.
Именно он поможет разработать интерьер и предложить различные модные
варианты отделки. Дизайнер составит проект, в который будут входить
технические чертежи. Это новое расположение стен с перегородками и
размеры пола и потолка, элементы освещения и т.д. Не стоит экономить на
услугах дизайнеров, так как многократные переделки значительно увеличат
не только дополнительные затраты, но и сроки ремонта затянутся. В итоге
сумма переплаты будет превышать оплату услуг дизайнера.
Необходимо определиться со стилем комнат, оформить дизайн каждой
комнаты отдельно. Лучше, чтобы каждая из них была уникальна в своем
стиле, но, в то, же самое время вся квартира соответствовала общему
дизайну.
С помощью дизайнера можно выбрать мебель и другие предметы
интерьера. Благодаря точному дизайнерскому решению стиль комнат будет
логически завершенным и не будет иметь лишних предметов. Стоит доверить
профессионалу покупку качественных материалов.
Также дизайнер разработает цветовую гамму комнат, подберет
интерьер квартиры до начала работ и впоследствии будет контролировать
процесс ремонта и вносить некоторые коррективы.
Например, в гостиной комнате, которая является визитной
карточкой хозяев, должны сочетаться следующие качества – это уют и
тепло. Данную комнату лучше всего приспособить для каждого члена семьи,
так как именно здесь проводится много времени.
Евроремонт спальни должен отражать индивидуальность и характер
хозяев, поэтому дизайнер поможет создать тот интерьер, в котором будет,
приятно и легко отдыхать. Спальня должна соответствовать вкусам своего
владельца.
Если евроремонт делается и в детской комнате, тогда можно
поэкспериментировать. Желательно учесть пожелания ребенка. В том случае,
если детей несколько, а комната одна, лучше всего разделить ее
перегородками, чтобы каждый ребенок имел свое личное пространство,
которое можно оформить в разных стилях. В оформлении интерьера детской
можно не придерживаться строгих правил, эти требования можно применить к
другим комнатам.
Выбор рабочей бригады.
Следующим этапом в ремонте квартиры будет выбор строительной
фирмы, которая обязуется выполнить свою работу на высоком уровне. Чтобы
квартира выглядела после евроремонта красиво и была функциональной,
лучше всего обратиться за помощью к опытным специалистам. Они обычно
организовывают работу быстро и качественно.
Чтобы найти хороших специалистов, можно обратиться к друзьям,
которым уже делался евроремонт, и которые подскажут название фирмы.
Другим вариантом может быть изучение каталогов и журналов, либо
интернет-объявлений.
Современные строительные компании имеют в штате опытных рабочих,
которые грамотно составят и сделают перепланировку будущего жилья.
Евроремонт квартиры – это, в первую очередь, исправление ошибок
предыдущих строителей, поэтому выравнивание стен и полов будет одной из
главных задач специалистов.
Основные этапы проведения строительных работ.
Евроремонт квартиры лучше всего начинать с перепланировки
неудобных комнат, ломки перегородок и стен. Подобные работы возьмут на
себя специалисты строительной фирмы. Они смогут правильно сделать проем в
бетонной стене и соорудить новую перегородку из высококачественных
прочных материалов. Следует максимально эффективно использовать
территорию квартиры, чтобы не осталось пустых и бесполезных мест.
Также не стоит путем перепланировки создавать узкие и длинные
помещения, лучше всего делать комнаты пропорциональными. Еще одним
важным элементом в ремонте должна быть минимализация углов и
использование арок.
Сегодня модным дополнением являются многоуровневые потолки,
которые придают интерьеру комнаты элегантности и создают дополнительное
освещение.
Дальнейшим этапом будет проведение электроработ. Сюда входят
ремонт проводки, замена розеток, поэтому строительная фирма обязательно
предоставит специалиста электрика. Ко всему прочему современные
строительные компании производят электрические работы без ломки стен.
Здесь стоит заранее продумать расположение розеток и выключателей.
Если полы находятся в плохом состоянии их следует заменить на
новые. Существует несколько вариантов: положить плитку, ламинат,
деревянные полы, паркет или ковровое покрытие. Кухню и ванную лучше
всего выложить плиткой, которая укладывается за несколько дней. Для стен
в кухне многие специалисты используют пластиковые панели, так как обои
не всегда являются практичным материалом.
Следующий шаг – это проведение отделочных работ. Отделка потолков
во многом определяет внешний вид комнаты. Это может быть монтаж
потолков из гипсокартона в нескольких уровнях или использование натяжных
потолков.
Современные дизайнеры используют декоративные отделочные
материалы для отделки стен: акриловые краски, фактурная или венецианская
штукатурка, а также пробковые покрытия или тканевые обои.
Немаловажным этапом является продумывание дизайна дверей, практичность их открывания и правильное расположение.
Настоящий евроремонт – это дорогая процедура, но, если
придерживаться золотой цепочки «дизайнер – строитель - интерьер», то
можно быть уверенным, что совершенные затраты сделаны удачно. Процесс
создания образа квартиры можно сравнить с музыкальным инструментом,
который идеально звучит. Здесь объединяются усилия проектировщиков,
дизайнеров и рабочих, которые умело потрудились над правильным звучанием
общего стиля квартиры.
25 февраля 2011
Приборы: металлические измерительные линейки; лопатка; круглый металлический стержень диаметром 16 мм, длина стержня – 600мм с закругленными концами, конус стандартный, технический вискозиметр.
Материалы: цемент, песок, щебень (гравий), вода.
Расчетный состав материалов на 1000 литров (1м3) бетонной смеси пересчитывают на объём 10 литров. Из полученного количества компонентов готовят пробный замес и определяют подвижность или жесткость полученной бетонной смеси.
Перемешивание производят в последовательности, приведенной ниже.
Отвешенное количество песка помещают в металлическое корыто. Корыто предварительно протирают влажной тряпкой, чтобы не было потерь влаги на увлажнение поверхностей. Затем добавляют требуемое количество цемента и перемешивают до получения смеси однородного цвета; после добавляют крупный заполнитель и всю смесь перемешивают до тех пор, пока щебень (гравий) не будет равномерно распределен в сухой смеси; в середине перемешанной смеси делают углубление, куда вливают половину отвешенной воды, осторожно перемешав, собирают материалы в кучу и добавляют остальную часть воды.
После этого энергично перелопачивают бетонную смесь до достижения ею однородности; длительность перемешивания составляет 5 мин.
После приготовления бетонной смеси определяют её подвижность с помощью стандартного конуса
Увлажнённый конус устанавливают на ровную площадку, становятся ногами на опоры, затем прижав конус к площадке, заполняют его в 3 слоя бетонной смесью, уплотняя каждый слой на всю толщину 25-тью штыкованиями.
Уплотненную смесь выравнивают лопаткой с верхним обрезом конуса, после чего поднимают его вертикально вверх и ставят рядом, измеряя расстояние от нижней грани линейки до верха бетонной смеси с точностью до 0,5см, определяем осадку конуса – подвижность бетонной смеси
Если подвижность бетонной смеси больше требуемой, то в замес добавляют песок и щебень, 5-10% от расчетного, в принятом соотношении. Путем нескольких попыток добиваются требуемой подвижности, после чего расчетный состав бетона корректируется и делается новый замес для изготовления трех образцов – кубиков.
При изготовлении бетонной смеси происходит как бы уменьшение общего объёма материалов, т.к. зерна песка располагаются между зернами щебня, а частицы цемента между зернами песка. Поэтому, если насыпать в определенную ёмкость цемент, песок, щебень, а затем начать их перемешивать, то будет получен объём бетонной смеси меньше первоначального объёма.
25 февраля 2011
Для ориентировочного определения составов смешанных (цементно-известковых) и цементных растворов, приготовляемых на портландцементе и других гидравлических вяжущих веществах, можно использовать табл.
Подбор состава сложного строительного раствора производится при наличии следующих исходных данных:
- назначения строительного раствора и условий его эксплуатации в конструкциях (влажность среды); - марки строительного раствора; - подвижности растворной смеси, выбираемой в зависимости от назначения раствора и условий его укладки; - вида вяжущего, выбираемого в зависимости от назначения раствора, его условий эксплуатации и марки раствора по прочности;
Составы растворов для каменной кладки
Марка цемента
|
Составы в
объёмной дозировке раствора марок
|
200
|
150
|
100
|
75
|
50
|
25
|
Цементно-известковые
|
50
|
1:0
2:3
|
1:0
3:4
|
1:0,
5:5,5
|
1:0,
8:7
|
-
|
-
|
400
|
1:0,
1:2,5
|
1:0,
2:3
|
1:0,
4:4,5
|
1:0,
5:5,5
|
1:0,
9:8
|
-
|
300
|
-
|
1:0,
1:2,5
|
1:0,
2:3,5
|
1:0,
3:4
|
1:0,
6:6
|
1:1,
4:10,5
|
200
|
-
|
-
|
-
|
1:0,
1:2,5
|
1:0,
3:4
|
1:0,
8:7
|
Цементные
|
500
|
1:3
|
1:4
|
1:5,5
|
1:6
|
-
|
-
|
400
|
1:2,5
|
1:3
|
1:4,5
|
1:5,5
|
-
|
-
|
300
|
-
|
1:2,5
|
1:3
|
1:4
|
1:6
|
-
|
200
|
-
|
-
|
-
|
1:2,5
|
1:4
|
-
|
- марки вяжущего, выбираемой в
зависимости от плотности раствора, насыпной плотности и влажности заполнителя;
- вида используемой минеральной добавки и её
свойств (плотности и подвижности).
Расход воды для получения растворной смеси заданной подвижности зависит от состава раствора, вида вяжущего и заполнителя. Его устанавливают в опытных замесах.
Далее рассчитывают состав раствора на замес требуемого объёма, приготавливают пробный замес, уточняют и определяют расход материалов на 1 м3 раствора.
25 февраля 2011
Керамическими называют искусственные каменные материалы, получаемые из глиняных масс путем формования, сушки и последующего обжига. После обжига керамические материалы приобретают значительную прочность, водостойкость, морозостойкость и ряд других ценных свойств.
Среди керамических материалов наибольшее распространение имеют керамический обыкновенный и пустотелый кирпичи, пустотелые керамические камни, облицовочные плитки, керамическая черепица и керамзит.
Керамический кирпич изготавливают из легкоплавких глин с отощающими добавками или без них, пластическим или полусухим способами прессования и с последующей сушкой и обжигом.
При пластическом способе, глину измельчают сначала в вальцах, а затем в глиномялке, где её увлажняют до 18-25% и перемешивают до получения однородной массы. Подготовленную массу подают на прессование в приемную ленточного пресса. Цилиндрический шнек пресса с лопастями проталкивает массу через мундштук. Масса уплотняется и выходит из мундштука в виде четырехугольного бруса. Затем получают кирпич - сырец заданной толщины, разрезая движущийся брус поперек, тонкими стальными проволоками резательного устройства.
При полусухом способе, подсушенную и мелкоизмельченную глину тщательно перемешивают и увлажняют до 8-12%. Прессуют кирпич-сырец на револьверных прессах под давлением до 15 МПа. Сушка кирпича-сырца осуществляется в сушилках, а обжиг - в туннельной печи непрерывного действия.
25 февраля 2011
Марка кирпича определяется по среднему и минимальному результату значений предела прочности при сжатии и изгибе.
Приборы: сферическая чашка, шпатель, стеклянные пластины, листовая бумага, совок, металлические линейки, емкость с водой, мерный цилиндр, технические весы и гидравлический пресс.
Материалы: портландцемент марки не ниже 300.
а) определение прочности при сжатии
Из портландцемента приготавливают в стальной чашке тесто, водоцементным отношением в пределах 0,24-0,30. Отобранные для испытания кирпичи распиливают дисковой пилой на распилочном станке на две равные части.
Перед изготовлением образцов, кирпич погружают в воду не менее чем на 5 минут. На лист из стекла кладут смоченный в воде лист бумаги, на который наносят цементное тесто толщиной около 4 мм и укладывают половинку кирпича. На верхнюю поверхность этой половинки кирпича также наносят слой цементного теста и сверху укладывают вторую половинку кирпича, излишки цементного теста на бумаге и шве срезают ножом.
Для выравнивания верхней поверхности образца вновь берут лист стекла с бумагой и тестом и, перевернув образец, укладывают его на это тесто. Толщина шва и выравнивающих слоев на верхней и нижней поверхностях образцов должны быть от 3 до 5 мм. Подготовленные образцы должны иметь взаимно параллельные поверхности и перпендикулярные к боковым граням
Допускается испытывать образцы, склеенные из целого кирпича. Изготовленные образцы выдерживают в камере нормального твердения не менее трех суток при температуре 20±30С и относительной влажности 90-95%. Измеряют линейкой ширину и длину каждой постели образца с точностью до 1 мм и вычисляют площадь как среднее арифметическое результатов измерений двух поверхностей. Образцы устанавливают в центре опорной плиты пресса. Нагрузка при испытании должна возрастать непрерывно со скоростью 0,15 МПа/с.
В течение 5 минут кирпич насыщают водой, после чего на верхней постели, в месте передачи нагрузки, и на нижней, в месте опирания кирпича на опоры, наносят из цементного теста полоски шириной 2-3 см и толщиной около 3-5 мм.
Полоски делают с помощью металлических линеек или шаблонов. В пустотелом кирпиче пустоты, которые попадают на опоры, перед нанесением на них полосок заполняют цементным раствором. Допускается вместо полосок поверхность образца подвергнуть шлифованию.
До испытания образцы выдерживают в помещении не менее 3-х суток при температуре +20 0С. Определяют высоту образца, как среднее арифметическое двух измерений боковых граней (исключая толщину выравнивающего слоя) и ширину – как среднее арифметическое значение двух измерений верхней и нижней граней.
Кирпич укладывают на две цилиндрические опоры диаметром 10-15 мм с расстоянием между центрами 20 см и нагружают сосредоточенным грузом в середине пролета. При испытании пустотелый кирпич укладывают пустотами вниз.
По усредненному значению предела прочности при изгибе определяется марка.
25 февраля 2011
Портландцемент - продукт тонкого измельчения клинкера с добавлением гипса (3-5%). Клинкер получают обжигом до спекания при t = 14500С сырьевой смеси, состоящих из карбонатных пород (75-78% известняков различного типа ) и глинистого сырья (22-25% - глины, шлаки, мергели ).
Портландцемент с заданными свойствами получают несколькими путями:
- регулируя минералогический состав и структуру цементного клинкера; - регулируя тонкость помола и зерновой состав цемента, вводя добавки.
В настоящее время применяются следующие виды портландцемента:
- быстротвердеющий; - гидрофобный; - пластифицированный; - сульфатостойкий; - пуццолановый; - шлакопортландцемент.
Выпускается портландцемент марками 300, 400, 500, 550, 600.
25 февраля 2011
Цементным тестом называется смесь цемента с водой. Определение водопотребности цементного теста сводится к определению количества воды, требуемого для придания тесту нужной пластичности. Эти данные нужны нам для определения сроков схватывания и равномерности изменения объёма.
Водопотребность цементного теста считается нормальной, когда пестик прибора Вика, погружаясь в кольцо с цементным тестом не достигает дна на 5-7 мм.
Пестик имеет диаметр 10±0,02 мм и длину 50 мм. Масса стержня с пестиком 300г. Кольцо прибора, в которое помещается цементное тесто, имеет форму усеченного конуса.
Приборы: приборВика сферическая чашка, лопатка, мерный цилиндр (стеклянный). Материалы: портландцемент.
400г цемента помещают в чашку, делают в нем углубление, куда в один прием вливают 100-120 см3 воды. Затем немедленно заполняют углубление цементом и через 30сек. Осторожно перемешивают, потом энергично растирают тесто лопаткой.
Продолжительность перемешивания – 5 минут с момента затворения с водой. Сразу после окончания перемешивания в один приём наполняют цементным тестом коническое кольцо прибора ВИКа, которое 5-6 раз встряхивают, постукивая пластинкой о стол. Затем поверхность теста сравнивают с краями кольца, срезая избыток ножом, протертым влажной тканью.
Если за 30 сек. Пестик не дошел до дна кольца на 7 мм , это означает, что при затворении цемента было взято недостаточное количество воды, если расстояние от пестика до дна стало меньше 5мм – воды при затворения было взято больше нужного. Изменяя количество воды, вновь повторяют опыт до тех пор, пока не будет получено цементное тесто необходимой водопотребности.
Сроки схватывания цементного теста характеризуются началом и концом схватывания.
В твердеющих бетонах и растворах при равномерном распределении объёма могут образовываться трещины. Они могут быть вызваны избытком в цементе свободных оксидов кальция и оксидов магния.
Равномерность изменения объёма определяется кипячением в воде цементных лепёшек. Из 300г цемента приготавляют тесто нормальной водопотребности. Отвешивают 4 навески цемента по 75г и руками придают каждой навески форму шарика.
Шарики помещают на стеклянные и металические пластинки, смазанные машинным маслом и легким постукиванием пластинки о стол превращают в лепёшки диаметром 7-8см и толщиной в середине 1см, потом движением смоченного ножа от края к центру приглаживают для получения острых краёв и гладкой закруглённой поверхности.
Цемент считается отвечающим требованиям равномерного изменения объёма, если на лицевой стороне, подвергнутой испытанию, не наблюдаются радиальных трещин, доходящих до краёв
|